PLC control, or Programmable Logic Controller control, is an electronic device that automates production and manufacturing processes, leading to higher productivity and lower costs. This simple building block can provide logical control of machines within a dynamic business. It consists of connected sensors and external controls that work with a central computer to make decisions based on preset rules. This provides companies with insight into their processes and can help increase productivity and reduce maintenance costs.
Table of Contents
History and development of PLC control
In the 1960s, companies started looking for a more efficient and flexible way for logical control of machines, which led to the great development of a new control technology. Programmable electrical control became the improved alternative to traditional relay-based systems. Since then, PLCs have played an important role in the advancement of industrial automation.
PLCs have become increasingly sophisticated over time and are available in many variations. This is accompanied by improved processors, memory capacity and communication functions. All in all, this enables broader applications, such as the control of production lines, packaging and gathering machines and the automation of buildings and infrastructure.
Programmable logic controllers (PLCs) today have advanced features such as real-time data analysis, integrated safety systems and integration with other industrial systems through the Internet of Things (IoT), allowing companies to simplify their automation processes.
The application areas of PLC control
PLC control has a wide range of applications, from factory production lines to transportation systems and infrastructure. In the industrial industry, PLC helps automate the control of production steps for greater efficiency and productivity. It is also used in the transportation industry to control aircraft, trains and traffic lights. Moreover, in some areas of the energy sector, PLC control helps automate and monitor processes. Therefore, this versatile technology is useful in many industries for increased efficiency and productivity.
OPEN CALCULATION
OFFER IN 5 DAYS
SUSTAINABLE INNOVATIONS
UL/CSA
AT HOME
The operation of PLC control
Explaining the components of a PLC system
A PLC system consists of several components that enable the automation of a process. The main components of the PLC system are described below.
- Processor Unit: The processor unit is the core of a PLC system and executes the programmed logic.
- Memory: Memory is where processes, information and intermediate results are stored.
- Inputs and outputs (I/O): I/O components (logic gates) connect the PLC system to external sensors and actuators that send and receive signals.
- Power Supply: The power supply component ensures that the PLC system has the required power.
- Communication interface: The PLC system can communicate with other systems, including supervisory and control systems, through a communication interface.
- Control panel: The control panel is the interface between the operator and the PLC system and provides access to the programming environment and data.
In combination, these components form an effective and versatile system that can automate and monitor processes. This allows companies to better control their production procedures.
How PLC control processes and controls information
PLC control enables efficient and precise automation of complex plants through the combination of hardware and software. The hardware includes sensors, actuators and the PLC itself connected to the process. The software includes rules and algorithms used by the PLC to analyze data sent by sensors and determine how to control the process. Commands are then sent to actuators that ensure that the process is actually controlled. This combination enables higher productivity at lower cost through improved automation efficiency.
Configuring and customizing PLC controls.
Configure and adapt PLC control to the needs of your production process. This can be done by modifying existing programs or integrating new components and sensors. For example, integrate sensors for humidity, pressure or temperature so that the PLC can monitor and analyze the data, resulting in a more efficient production process. Further increase efficiency by adding graphical displays, buttons and other control components to enhance the user interface. Personalization of the PLC control ensures that it meets your unique requirements, increasing productivity. So if you are looking for an automated solution that is flexible and powerful, consider PLC control. If you have questions about the right PLC controller, you can always contact us.
Contact our experienced innovator
Cees Brasser
With more than 26 years of experience at the helm of Gerbin Control, Cees Brasser is your expert on panel construction for the machinery sector. Discover how his knowledge and insight can take your project to new heights. Get in touch now!
The benefits of PLC control
Control with a programmable logic controller has several advantages over traditional control systems. Below we give you some of them:
- Flexibility: PLCs can be programmed to control different processes and can be adapted to changing production requirements.
- Monitoring and analysis: PLCs enable real-time monitoring and analysis of production processes, identifying potential problems early so they can be proactively resolved.
- Safety: PLCs provide advanced safety systems, including emergency stops and protection relays, to improve safety and reduce the risk of accidents in a work environment. This also ensures and safe condition in the long run.
- Cost-effectiveness: The use of PLCs is generally more cost-effective than traditional control systems because they require little maintenance and pose less risk of failure.
PLC control provides companies with powerful and versatile automation and monitoring solutions that can lead to increased productivity, efficiency, safety and controllability.
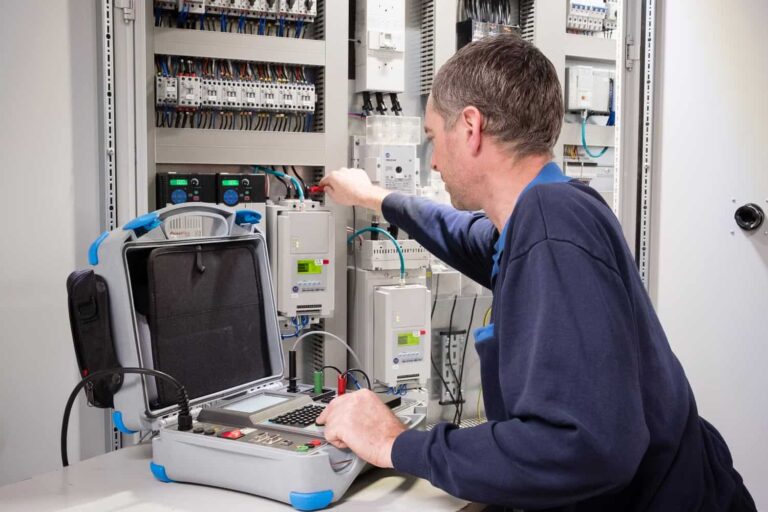
Tips for extending life
For a reliable and efficient production process, it is important to extend the life of your PLC control system. Here are some tips you can look out for:
Regular maintenance: Regular maintenance of the PLC control system is essential to extend its life.
Protect from dust and moisture: To maintain the integrity of your PLC control system, it must be kept away from dust and moisture. A dust screen may be needed to provide additional protection.
Avoid overloading: Overloading your PLC control system can cause fatigue and damage. Carefully adhere to the recommended load limits to avoid this.
Use quality components: By including quality protection relays and power protectors in your PLC, you can also extend its life.
Your electrical engineering ambitions, our mission
Our expert team at Gerbin Control is ready to turn your electrical issues into concrete solutions. Are you ready for the next step?
Regular maintenance of PLC controls
Last but not least, regular maintenance of PLC controls is important for reliable and efficient production. The PLC system is at the heart of many modern production lines and machine fleets, helping to achieve optimal performance and product quality. Regular checks for software updates, defects and diagnostics of the system should therefore be performed regularly to avoid problems. For this, always get information from a specialized company.
Related Articles
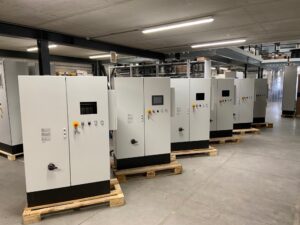
What trends in panel building can we expect for 2024?
The world of panel building is one of constant evolution and innovation. As technology advances, market expectations are increasing. But what trends in panel construction can we expect for 2024? At Gerbin control, an industry leader in producing high-quality electrical panels, we took a look at what the future holds for us.
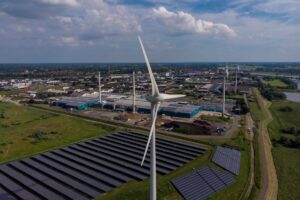
The role of reuse in panel building within the circular economy
When building modern infrastructures and systems within industry, panel construction plays a crucial role. But have you ever wondered how panel construction can contribute to

The importance of certified panels for safety and quality
In an era where technology and innovation go hand in hand, Gerbin Control has established itself as a leading panel builder. Safety and quality are
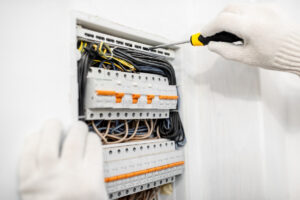
Are energy-efficient panel systems the key to a better planet?
In a world where sustainability is no longer a luxury but a necessity, we are constantly looking for ways to reduce our carbon footprint. One
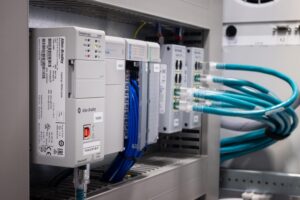
The best choice of materials for durable panel construction
If there is one thing we are passionate about at Gerbin Control, it is the innovation and quality that goes hand in hand with sustainable panel construction. When choosing the best materials for panels, there are several factors to consider. In this article, we dive deeper into those choices, drawing on our years of experience in the industry.
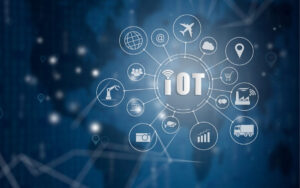
How panel systems are the bridge to the Internet of things
At Gebin Control, we recognize the revolutionary power of panel systems and their integration into the emerging world of the Internet of Things (IoT). In